sheet metal
sheet metal fabrication for your custom parts
About team
How Does Sheet Metal Fabrication Work?
Sheet metal fabrication involves the creation of objects from thin sheets of metal through cutting, bending, and forming processes. The process typically starts with selecting metal and cutting it into the desired size and shape. The metal is then shaped using various techniques like rolling, extruding, bending, and welding to form the final product. Sheet metal fabrication can include everything from simple shapes to complex designs, with each part going through cutting, bending, surface treatment, and assembling steps to achieve the desired end product.
The completion of a product usually involves multiple steps, from cutting and bending to surface treatment and assembling, with a variety of fabrication techniques used based on costs and needs. Common processes in sheet metal fabrication include cutting (laser cutting, water jet cutting, plasma cutting), bending (using press brakes), punching (creating holes in sheets), welding (joining components), and assembling (using fasteners or welding)
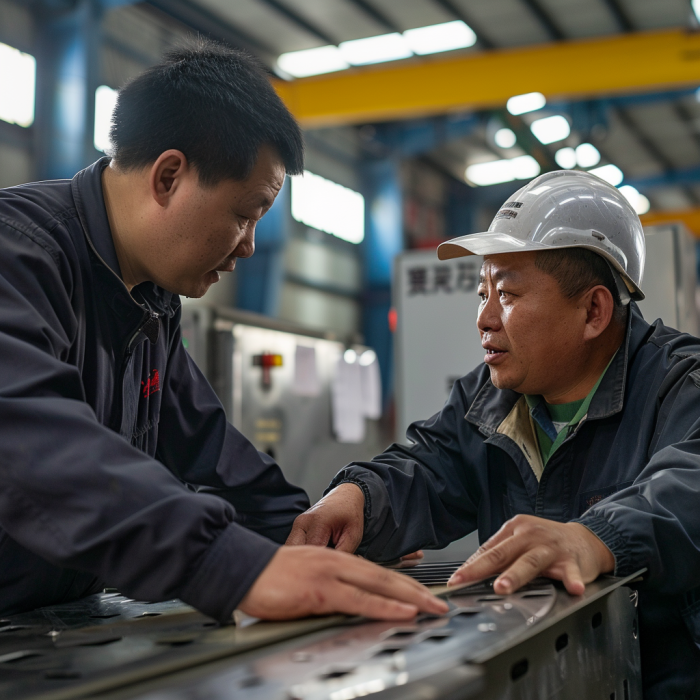
check our parts
see our products
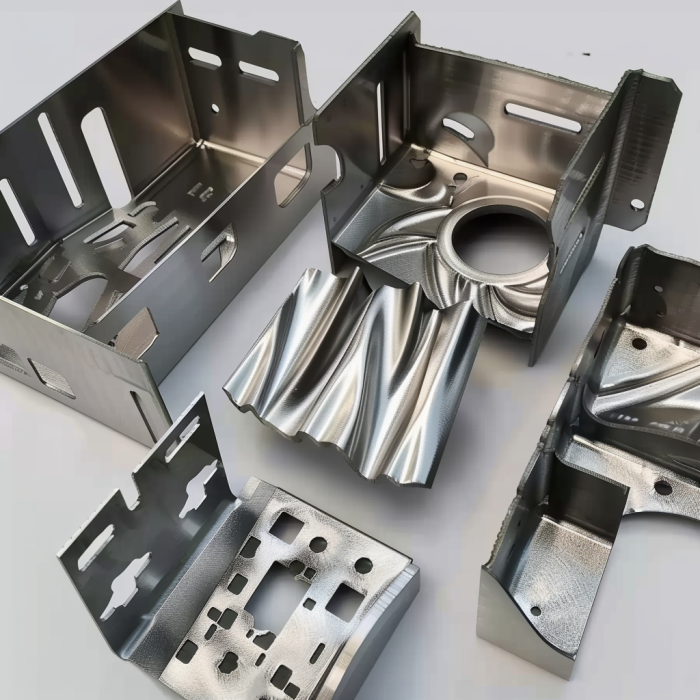
stainless steel parts
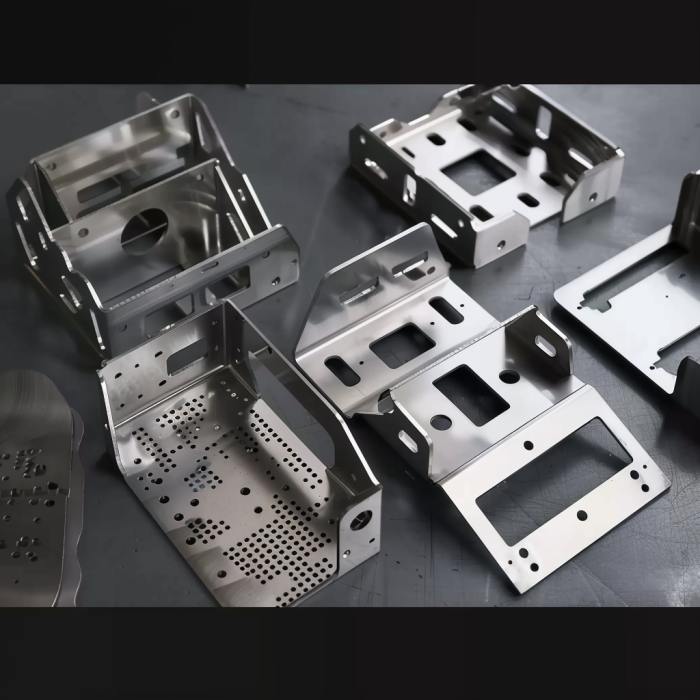
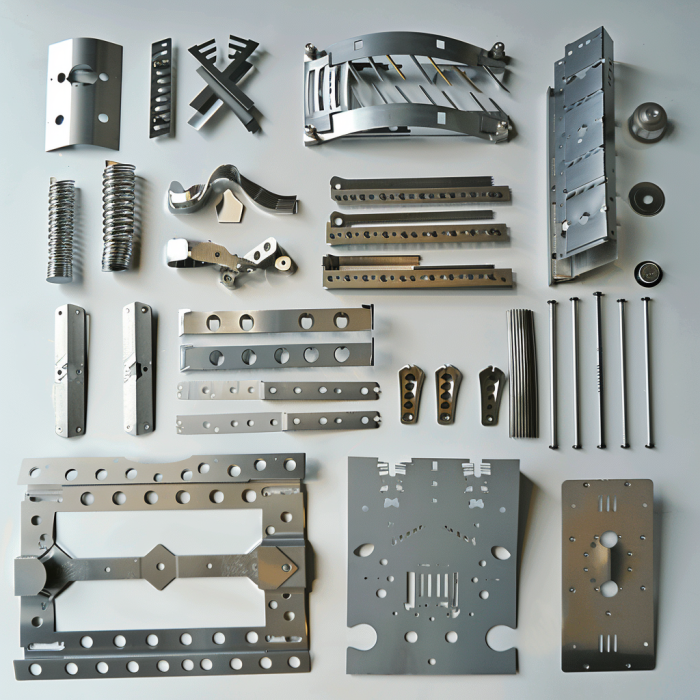
Fabrication Techniques
Sheet metal fabrication is a comprehensive process that transforms raw sheet metal into functional parts and products through various techniques.
Cutting is a fundamental step in sheet metal fabrication. Advanced technologies like laser cutting, waterjet cutting, and plasma cutting allow for precise shaping of metal sheets. Laser cutting uses a high-powered laser beam to melt the metal, offering high precision and clean edges. Waterjet cutting employs a high-pressure stream of water, possibly mixed with abrasive particles, making it ideal for materials sensitive to high temperatures. Plasma cutting, on the other hand, is suited for cutting thick metal sheets by using a plasma torch to heat the metal to a molten state.
Bending is another critical technique where force is applied to the metal sheet to create bends, producing V-shapes, U-shapes, and channels. This process is essential for constructing metal frameworks and enclosures, enabling the creation of complex shapes and structures.
Punching involves removing parts of the metal sheet to create holes or cutouts, a process typically performed with a punch press. It’s particularly useful for creating ventilation grates, panels, or components requiring specific hole patterns.
Welding is the process of joining two metal parts together, a pivotal step in many sheet metal fabrication projects. Various welding techniques can be employed, depending on the material and the desired strength of the joint, including MIG welding, TIG welding, and spot welding. This process not only ensures the structural integrity of the fabricated parts but also allows for the construction of complex assemblies from simpler components.
Together, these techniques form the backbone of sheet metal fabrication, enabling the production of durable, high-quality metal parts and products tailored to diverse applications.
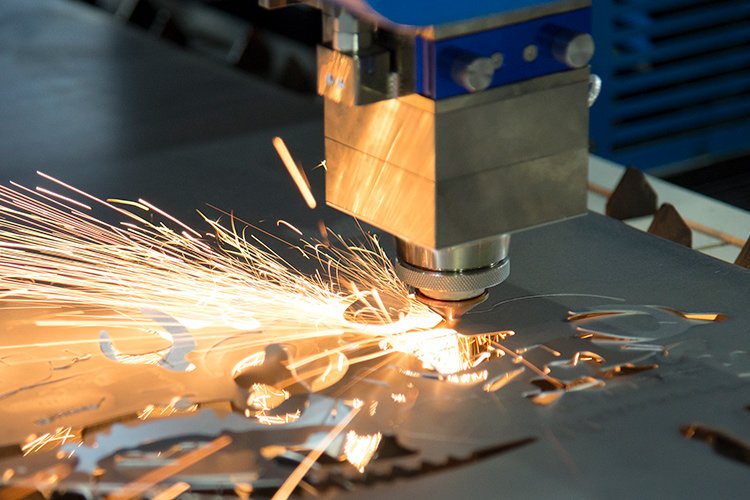

Advantages of Using Sheet Metal
Sheet metal is celebrated for its versatility, durability, and cost-effectiveness across numerous industries. It’s easily fabricated into complex shapes, withstands harsh conditions, and supports efficient high-volume production. Additionally, its lightweight and aesthetic adaptability make it a go-to material, fueling innovation and enhancing product longevity and appeal.


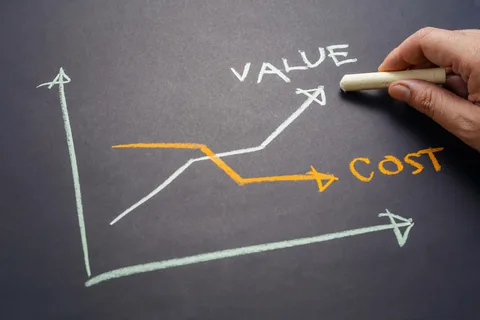

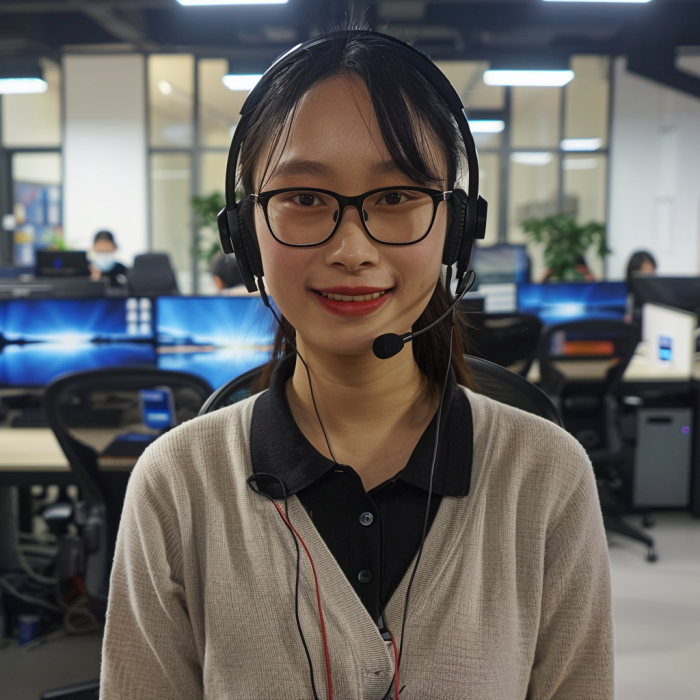
Send us a message
Your satisfaction are at the heart of everything we do.contact us now , we are here all the time.