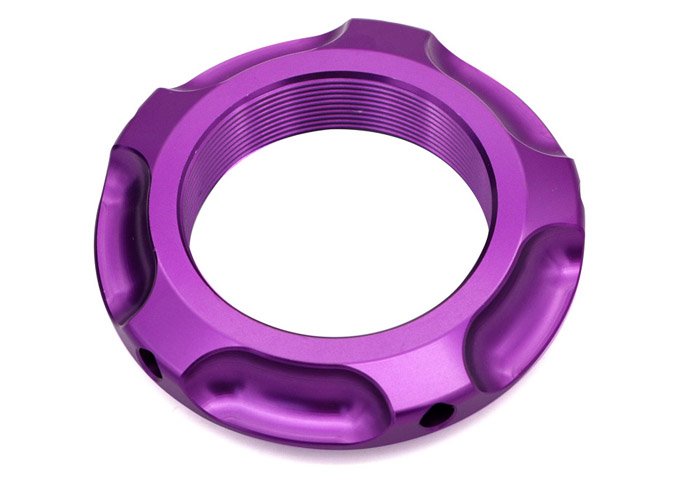
Corrosion Resistance
Anodized aluminum parts offer exceptional corrosion resistance, making them perfect for harsh environments. The anodizing process forms a protective oxide layer on the aluminum’s surface, shielding it from moisture, salt, and other corrosive elements. This durability makes anodized aluminum ideal for outdoor use, marine settings, and industries with chemical exposure.
Durability
The anodizing process greatly enhances the surface hardness of aluminum, increasing its durability and wear resistance. This improvement ensures that anodized aluminum parts can endure heavy use and mechanical stress without deteriorating. This is especially critical for industries like aerospace, automotive, and manufacturing, where parts face high friction and impact.
Aesthetic Appeal
Anodizing enables a wide range of colors and finishes, enhancing the visual appeal of aluminum parts. By adding dyes during the process, a variety of colors can be achieved, allowing for customization to meet specific design requirements. This makes anodized aluminum a popular choice in consumer electronics, automation, and automotive applications where aesthetics are vital.
Cost-Effectiveness
Despite the initial cost, anodizing proves to be cost-effective due to long-term benefits like reduced maintenance and extended lifespan. Anodized aluminum parts demand less frequent upkeep and replacements thanks to their enhanced durability and corrosion resistance. This results in significant cost savings over time, making them an economically viable option for many industries.
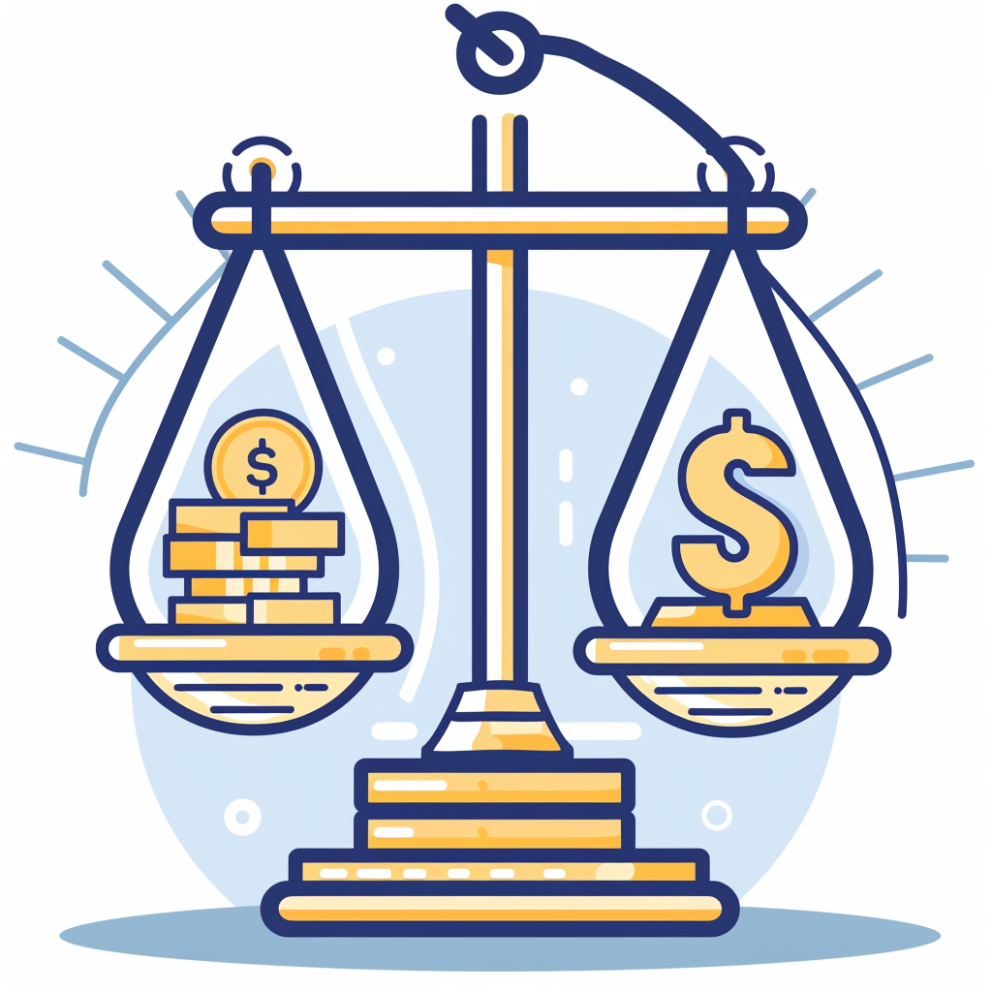
Thermal Conductivity
Anodized aluminum retains excellent thermal conductivity, crucial for applications needing efficient heat dissipation. This property is especially advantageous in electronics and automotive industries, where managing heat is vital for performance and preventing overheating. The efficient heat dissipation of anodized aluminum prolongs component life and enhances overall system reliability.
Electrical Insulation
The anodized layer offers electrical insulation, beneficial for electrical and electronic components. This insulating property is achieved without sacrificing the thermal conductivity of aluminum, making it ideal for parts requiring both heat management and electrical isolation. This dual functionality is advantageous in applications like power supplies, heat sinks, and electronic enclosures.
Improved Adhesion
Anodizing creates a porous surface that enhances the adhesion of paints, adhesives, and lubricants, making it perfect for further processing. The microscopic pores formed during anodizing improve bonding with coatings and treatments. This characteristic is valuable in manufacturing processes requiring additional layers of protection or aesthetic coatings.
Environmental Considerations
Customization Options
The ability to customize the thickness of the anodized layer and color options provides greater flexibility in design and application. This customization allows anodized aluminum parts to be tailored to meet specific performance and aesthetic requirements. Whether for increased corrosion resistance, precise color matching, or enhanced mechanical properties, anodizing offers a versatile solution for a wide range of applications.
Regulatory Compliance
Anodized aluminum parts frequently comply with various industry standards and regulations, making them suitable for critical applications. Adherence to standards such as ASTM, ISO, and MIL-SPEC is crucial for parts used in regulated industries like aerospace, medical devices, and defense. The anodizing process can be precisely controlled and certified to meet these stringent requirements, ensuring quality and reliability.
Is Anodizing Right For You?
Contact us for a free quote and project review! Our experts will advise on various finishing services for rapid prototypes and low-volume manufacturing. We’ll help you find solutions that fit your budget, timeline, and desired results. Let’s get started today!